There aren’t many places on Earth as remote, inaccessible and dangerous to reach as Rubaya. Here, deep in the green hills of Masisi territory, nearly 60 km from Goma in eastern DRC, roads are crumbling and bridges collapsing. But still, scores of people come here every day to join the group digging in the mud. If metals or minerals come from Rubaya, it’s hard to know whether they were extracted by industrial, or artisanal miners (many of whom, because of red tape or outright corruption, go months without being paid for their work or discoveries).
A new digital technology is hoping to change that. A barcode system, developed by supply-chain auditor RCS Global, was recently introduced at Société Minière de Bisunzu’s (SMB) local coltan mine. Using a handheld, cloud-connected mobile device, government agents tag and scan the barcode, and then upload data to the cloud, including the bag’s weight, and when and by whom it was tagged. According to Ferdinand Maubrey, RCS Global MD (Upstream), ‘it allows purchasers of SMB material to be sure that it actually comes from that mine site and is not smuggled into the supply chain from other mines, as much as possible’.
The idea of a handheld scanner is not new to mining. Across the world, miners have been developing and deploying digital technologies on-site for the past few years. Robotics, smart sensors, the internet of things (IoT), big data… They may be novel, but they’re nothing new.
IoT, for example, is now widely used to control mobile vehicles, keep tabs on employee movements and monitor underground air quality. And – as Karien Bornheim, CEO of Footprint Africa Business Solutions, explains – IoT offers an integrated solution for the industry.
‘To fully harness the business potential of IoT, the mining sector has to understand precisely how it can add value,’ she says. ‘IoT needs to be implemented across the entire value chain in order to deliver fully optimised, relevant and turnkey operational solutions. It doesn’t matter how large the project is, or how complex. What matters is that it is done in line with business strategy and with a clear focus.’
That is new. Deloitte’s 2020 Tracking the Trends report notes that although some firms have made strong technological advances, ‘many mining companies have yet to achieve the full benefits (or any value at all) of intelligent mining. […] While many companies have articulated a clear digital strategy, few have adopted the organisational changes needed to deliver on that strategy’.
Bornheim adds that the cross-pollination of different data sets from across various mine sites can help shift the dynamics in plant operation and maintenance. ‘In addition, with sensors and connected devices and systems, mining operations can be managed intelligently to ensure the best results from equipment and people,’ she says.
‘You can use IoT platforms to visualise mission-critical data for device monitoring, remote control, alerts, security management, health and safety, and healthcare. The sky is genuinely the limit, especially now that the cost of sensors has come down and the intelligence of solutions and applications has gone up. From real-time insights to hands-on security and safety alerts, to data that changes business direction and focus, IoT brings a myriad of benefits to the table.’
PwC, in a 2019 report, emphasises that ‘digitalisation is a fundamental part of the new business model, encompassing and affecting all areas of business: supply chains and operations, marketing and sales, and interactions with current and potential customers’.
It is, in other words, no longer a case of connecting this or that piece of equipment, but rather of transforming the supply chain from a series of largely discrete, siloed steps to what PwC’s landmark 2016 Industry 4.0 report describes as ‘a completely integrated ecosystem that is fully transparent to all the players involved – from the suppliers of raw materials, components and parts, to the transporters of those supplies and finished goods, and finally to the customers demanding fulfilment’.
Hence the cloud-connected tagging devices at SMB’s Rubaya coltan mines. And hence, too, why Anglo American Platinum has issued digital tablets to people on the front line to capture and upload workplace information to a central platform and facilitate timely responses. By 2018 Amplats already had more than 200 devices underground at its Dishaba mine.
In South Africa, Sibanye-Stillwater is among the leaders in the digitalisation of the full mining value chain – as evidenced by its involvement in Wits University’s DigiMine mining laboratory. ‘You don’t know what you don’t know when it comes to these new technologies such as 3D printing, blockchain, cloud computing and artificial intelligence. But there is a generation that is coming through the ranks that embraces it, and it becomes completely natural to them,’ according to Sibanye-Stillwater CEO Neal Froneman. For him, safety is the main driving force behind digitalisation. ‘I have got to start with safety,’ he says. ‘In my view – and I’ve said it publicly – unless we can really make a difference to safety and reduce the risk, I have to question whether we can morally keep on mining.’
That sense of morality is, to some extent, also behind the broader move to digitalise – and trace – products throughout the supply chain. Louise Mercer, chief customer experience officer at blockchain developer Everledger, explains the thinking behind this in an online post. ‘Shareholders and customers – especially millennials and independent women, two major markets for diamond jewellery – are increasingly motivated by sustainability,’ she writes.
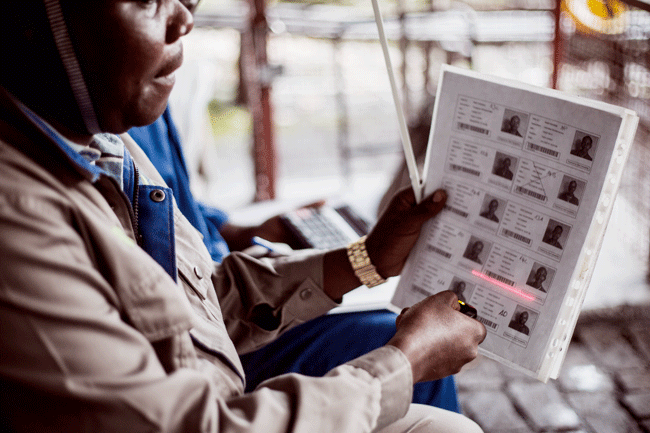
‘Transparency enables visibility over how sustainable a diamond is, as its full life cycle is immutably recorded on the blockchain. However, doing the right thing isn’t enough from a commercial perspective. You need to prove that you are doing it. Blockchain solutions facilitate tracking from mine to consumer, enabling easier compliance against increasingly strict measures.’
Mercer says that, by exposing the whole journey of the diamond (or the coltan, or whatever other mineral is being tracked), supply-chain monitoring also protects against unfair trade and unethical sourcing. Referring specifically to diamonds, she says that ‘this allows buyers to be more knowledgeable about their purchase in order to avoid the pitfalls of diamonds that don’t meet Kimberley Process standards or originate from conflict zones’.
Yet it’s not just about millennials Instagramming their ethically sourced earrings: major automotive and electronics firms are also under pressure to prove the provenance of the metals used in their laptops, e-vehicle batteries, video-game consoles, and so on. In early 2020 Volvo Cars joined IBM, Ford, Volkswagen and Huayou Cobalt, among others, in the Responsible Sourcing Blockchain Network (RSBN) consortium, which aims to track ethically sourced minerals used in EVs. The RSBN tracks cobalt from Huayou’s mine in the DRC all the way to the end manufacturer via blockchain.
As IBM spokesperson Hannah Slocum told Supply Chain Dive, ‘initially, the miner – in this case Huayou – will add data into the blockchain at the point cobalt is bagged and tagged. For key events like smelting, refining, etc, the inputs and corresponding outputs are added to the blockchain. With a trusted participant entering provenance data on to the blockchain […] supply-chain participants can know the percentage of cobalt that is verified to meet the guidelines and, in turn, ensure their downstream partners that they too are following these guidelines’.
Blockchain is not perfect (it is, after all, merely a ledger, open to as much fraud as any other), but the trend towards digital supply-chain management is nevertheless encouraging. For manufacturers, it offers reassurance that the minerals used in their products are ethically sourced. For miners, digitalisation enables greater safety at the proverbial coalface, closer management of equipment across an integrated system, and – in mines across Africa and the world – some measure of guarantee that the minerals in the supply chain are not tainted by corrupt or illegal mining.